Manufacturing Throughput
by Jason Bullard, on Feb 13, 2024 4:41:17 PM
How to avoid throughput overprocessing while optimizing efficiency and productivity
In manufacturing, throughput is frequently viewed as the ultimate expression of operational success, a reflection of how well your process and your people are performing. Today, growing numbers of manufacturers have access to powerful new tools and technologies that are changing the game and giving professionals new ways to boost efficiency, ultimately increasing throughput. But this quest is not without potential pitfalls—and even the most exciting new technology solutions need to be leveraged correctly to avoid potential issues.
For example, one common misstep many manufacturers make is engaging in throughput overprocessing: essentially overcomplicating production processes in a manner that is excessive, potentially wasteful, and ultimately counterproductive.
Avoiding throughput overprocessing starts with a consistent process. Consistency and repeatability are critical prerequisites for sustained efficiency and operational optimization. First time quality (FTQ) metrics can subsequently be monitored to help ensure consistency. And if those numbers are falling short, manufacturers can use the capabilities of connected process control solutions to conduct a root cause analysis and make procedural changes to correct any issues.
Operator Perspective
For operators, avoiding overprocessing means modulating the ways they engage with digital systems. If there is too much interaction (for example, if the operator is cued to constantly press an “OK” button to proceed), the result is wasted time and procedural bloat that ultimately adds zero value to the billable product. Today’s systems should complement and work with operators as a tool, not as a burden.
Priorities that build efficiency and promote ease of use include:
- Building out a consistent process—complete with visual aids of what to do and when to do it, with no room for ambiguity.
- Making sure equipment is triggered at the right moment for operator interaction. From pick lights, scanners, and torque tools to monument machines such as milling machines and test benches, the goal isn’t just to utilize tools, but to optimize them. Collecting and leveraging data helps ensure products are always built correctly and operators are not left guessing what to do next.
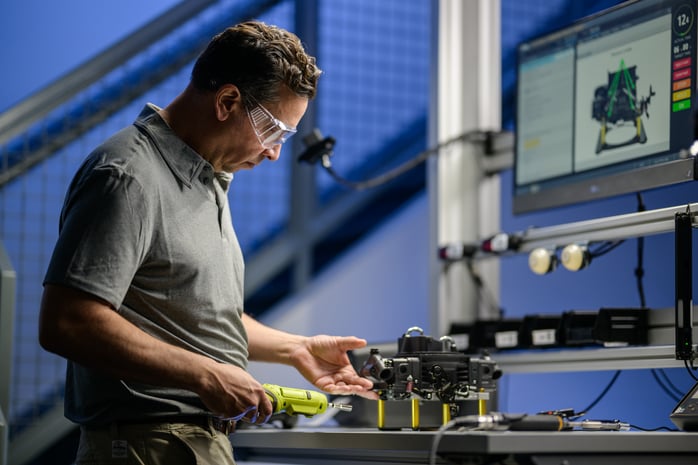
- Establishing clear reject and repair instructions that instantly direct operators the moment a problem occurs. The system should walk operators through the entire process to correct the issue, while digitally recording fault codes for subsequent analysis.
Engineer perspective
The engineer’s role is critical—thoughtfully creating and strategically refining processes, while avoiding throughput overprocessing and offering proper guidance for operators.
Engineering priorities include:
- Evaluating the work environment for operator efficiency and ergonomics. Something as simple as changing part or product location to be in arm’s reach or reconfiguring the geometry of the space can make an enormous difference.
- Digitizing real-time data collection for your part reporting (lot traceability as well as marriages of subcomponents).
- Building an effective fault management process. When the systems detect an error, they should guide the operator through a pre-configured reject or repair process.
- Avoiding overburdens by making use of accurate time and cost studies. The best of today's connected process control solutions collect time all the way down to the task level. This creates a better understanding of task resequencing and line rebalancing needs. For example, one recent Epicor customer was able to use digital guidance to increase throughput by 50%.
Manufacturers can see the impact of optimized throughput efficiency not just in KPIs, but in both upstream and downstream measurements—everything from resource utilization to customer satisfaction and profitability. Avoiding throughput overprocessing really boils down to giving operators everything they need to do their job more effectively—and nothing they don’t. It’s about empowering operators to efficiently complete all the steps they need to perform a task without redundancies or inefficiencies. Connected process control can help avoid throughput overprocessing and lead to improvements in quality, efficiency, and synergy, along with the ability to constantly evaluate and reevaluate to drive the most consistent results.