Identifying the 8 Lean Manufacturing Waste in Your Organization
by Tina Kennedy, on Mar 12, 2020 11:10:09 AM
Lean manufacturing is a management philosophy that provides tools and processes designed to eliminate waste from the manufacturing process, resulting in greater efficiency, efficacy and profitability for the organization.
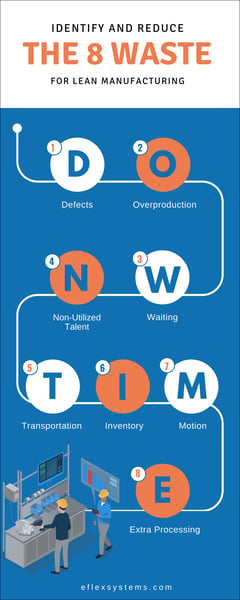
Defects
Overproduction
Waiting
Non-Utilized Talent
Transportation
Inventory
Motion
Extra Processing
While the principles behind lean manufacturing are simple enough to grasp, correctly identifying the wastes within your organization can prove a much more difficult task. As a recognized industry leader in the design and implementation of advanced technology and digital solutions for process control, eFlex Solutions has more than 30 years of experience tackling manufacturing waste on a global level.
Here are just a few examples for each of the eight wastes in lean manufacturing.
Defects
In lean manufacturing, a defect refers to a finished product deviating from your customer’s expectation, or its original standards of design. Defects can lead to rework, recalls and scrap—equating to waste in time, labor and resources. Among the eight wastes, defects are easiest to identify, since your customers or downstream process owners will likely alert you to the issue.
Examples of defects in lean manufacturing include:
- Worker does not accurately follow work instructions
- Worker fails to follow the quality inspection process
- Product is mistakenly shipped to the wrong customer
- Inventory level of specific manufacturing material is inaccurately recorded
Overproduction
Overproduction occurs when products are created before demand for it is generated. This can cost your organization money, unnecessarily tie up resources and balloon into other wastes like inventory and transportation. As a solution, many manufacturing facilities have adopted just-in-time manufacturing (JIT), a methodology aimed at reducing flow times within production systems and response times from supplier to customer, leading to increased productivity and lower cost.
Examples of overproduction in lean manufacturing include:
- Unstable production scheduling
- Inaccurate forecasting and demand information
- Overstaffed warehouses and production facilities
- Warehouse filled with product that does not sell or has not sold
Waiting
Another easily identifiable waste and the product of poor process design, is waiting. Waiting occurs whenever processes, people or goods are not moving through the system, resulting in lost time that ultimately affects the bottom line. Waiting can also trigger a catch-up mentality that may lead to defects as a result of shortcuts being taken. While the opposite of overproduction, this waste can be resolved through largely the same measures.
Examples of waiting in lean manufacturing include:
- Unplanned/unexpected downtime or idle machinery
- Human-caused delays, including internally or by a supplier
- Pausing activity while an automated machine finishes its task
- Holding production while a roadblock in the step ahead gets resolved
Non-Utilized Talent
One of the most damaging wastes of all is that of human potential. Failure to put the right people in the right seat in your organization can lead to high turnover, lack of motivation and total disengagement. Additionally, lack of proper process training can lead to high rates of human-caused error. There are a variety of technologies, management styles and training methods that genuinely engage employees—allowing people to work efficiently, voice and enact ideas and improve overall operational effectiveness.
Examples of non-utilized talent waste in lean manufacturing include:
- Idle or misused machinery
- Undertrained/mistrained labor
- Weak or non-existent career development program
- Lack of communication between leadership and staff
- Workers spending time on tasks that don’t add value
Transportation
The process of moving materials from one location to another, transportation is one of the most common areas of lean manufacturing waste. Transportation waste adversely affects several other wastes—including motion and waiting—resulting in high overhead costs, unnecessary expenditures and irregular production flow. Value stream mapping and changes in factory layout/production are just two ways to help allay this waste.
Examples of transportation waste in lean manufacturing include:
- Poorly coordinated logistics team
- Inadequate plant/production design
- Moving equipment between distant facilities
- Using a faraway supplier in lieu of more local providers
Inventory
The waste of inventory happens when product is created disproportionate to demand. Often a symptom of overproduction, inventory issues can prompt unnecessary storage costs, lead to wasted transportation and motion and signal a breakdown in process between manufacturing and purchasing. As a fix, advances in manufacturing technology have made it easier than ever for organizations to create products only as dictated by demand.
Examples of inventory waste in lean manufacturing include:
- Machinery that is seldom/never used
- Storage of parts or product that are expired/no longer needed
- Ordering additional parts or tools to replace damaged or outdated ones
- Overstocking in a way that does not meet the needs of your customer/doesn’t add value
Motion
Similar to transportation, the waste of motion extends to unnecessary activity within the workplace. Whether it’s through human error or outdated process/technology, this waste can be hard to identify because—while the potential for improvement is almost infinite—the acts are often too frequent/ingrained to be tracked, addressed or directly correlated to negative results. Technological tools and innovations have been found to have a profound impact on minimizing motion waste when successfully adopted by organizations.
Examples of motion waste in lean manufacturing include:
- Reactive maintenance
- Poorly located supplies or equipment
- Excessive machine movement/wear-and-tear
- Processes that take lengthier steps than actually needed
- Excess activity such as a worker searching for missing tools, work instructions or bending over to pick something up
Extra Processing
Like motion waste, extra processing involves adding further complexity to a product or process than is necessary to reach a desired value for your company and/or customers. Over time, these redundancies and exaggerations can add up to significant wasted time, money and talent. The use of modern tools, technologies and processes can drastically reduce processing time and help your organization reach maximum efficiency and efficacy.
Examples of extra processing waste in lean manufacturing include:
- Unclear specification or quality standards
- Installing a part or feature without testing demand
- Slow or multilayered decision-making and approval processes
- An overabundance of product or feature options for what the customer needs
For more than three decades, eFlex System has been supporting lean manufacturing philosophies to help organizations minimize waste and maximize value for their customers, their employees and their bottom line. Our highly evolved, Industry 4.0 technologies and tools allow for easy integration into the assembly process, optimal workplace training methods, industry-leading quality management and much more.