Digitalization Pitfalls
by Jason Bullard, on Jan 25, 2024 10:44:23 AM
How to safeguard your smart factory from costly errors
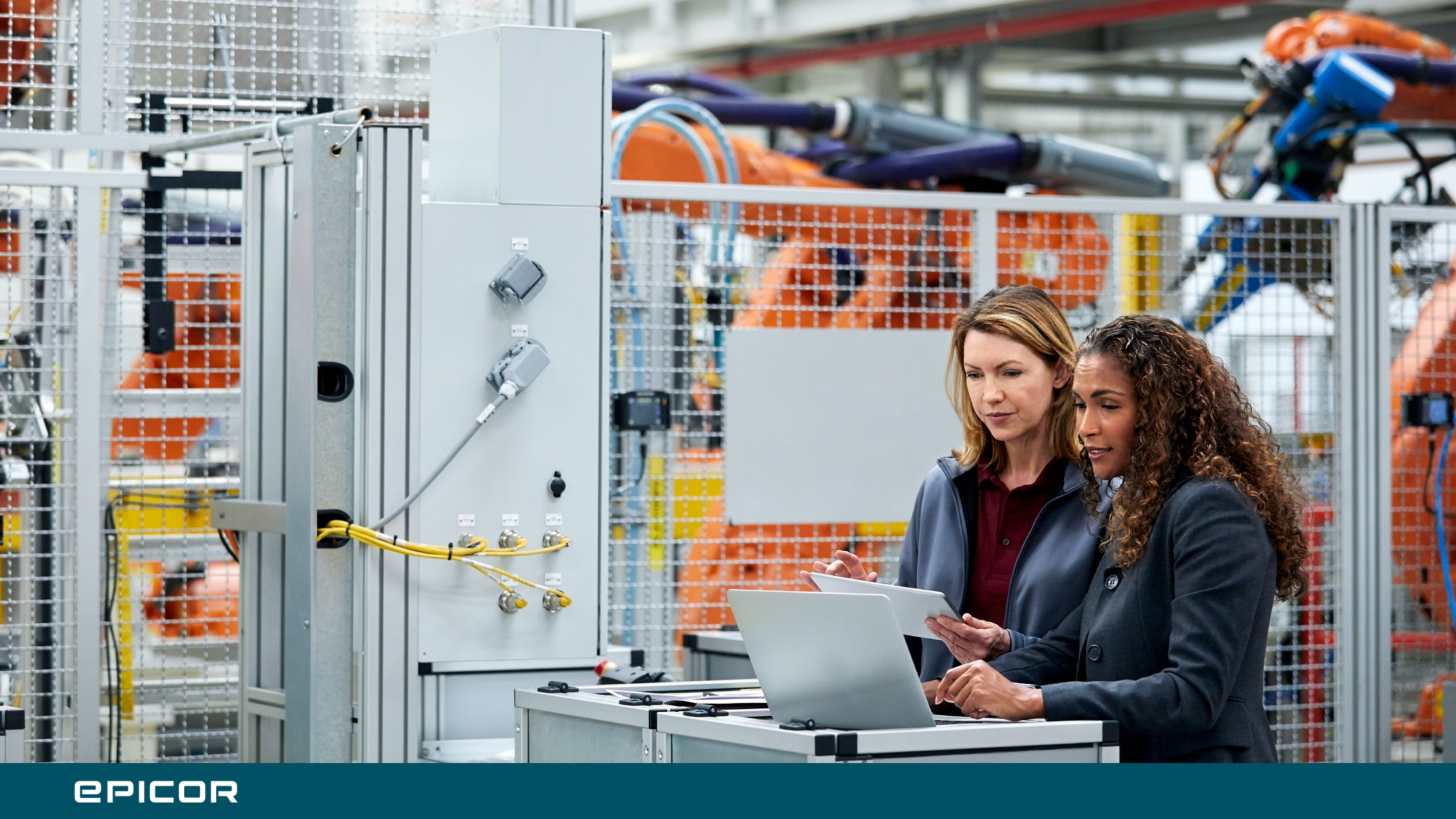
Growing numbers of manufacturing decision makers are recognizing that a successful digital transformation not only confers a competitive advantage but is increasingly viewed as a necessity in today’s marketplace. The improvements in efficiency, productivity, traceability, and error reduction made possible with a digitally connected factory are significant and often dramatic. But getting to that point isn’t always easy—especially for those who enter the digital transformation process without an organized approach.
In order to avoid some of the most common and costly mistakes that manufacturers are prone to making when executing a digital transformation, it’s essential to identify and sidestep these common digitalization stumbling blocks.
Failure to clearly define processes
Unlocking the true power of connected process control begins with a clear understanding of the day-to-day processes in your business. This does require work on the front end to create a digital copy of the operator's standard operating procedures (SOPs); however, this will set the foundation for a successful digital transition. Without absolute procedural clarity, designing the architecture of a connected process control solution becomes significantly more difficult—or even impossible.
Setting out for the finish line without knowing the route
Problems are often relatively easy to identify, but solutions tend to be somewhat less simple. For example, if you are not hitting your shipping targets, you might be inclined to add operators or labor. However, there may be inefficiencies in your process that are not labor-dependent. By having a connected process control system in place, you are able to identify those inefficiencies and pinpoint improvement initiatives to meet the desired targets.
Eating the elephant
The complexity of some digital transformations can feel like an intimidating and even overwhelming process. Sometimes out of mistaken enthusiasm, manufacturers tend to feel that they need to encompass 100% of the entire process before they deploy on the plant floor. With connected process control in place, it’s easy to start small in areas of impact. This allows operators time to understand their interaction with the system before scaling to other areas. Experienced companies in this space understand the importance of “going fast by moving slow”—approaching the digital transformation process in a deliberate, strategic, and incremental manner. Don’t eat the elephant in one gulp. Instead, move forward one bite at a time, making small changes that build over time.
Not empowering a champion
Outside expertise can provide critical counsel and guidance throughout the digital transformation process. But it’s just as important to designate an internal “champion” who is responsible for overseeing the design and rollout of new digital systems and solutions. This individual should have extensive knowledge of the processes and products, along with the power to make changes as needed.
Neglecting your culture
A positive and supportive internal culture surrounding these changes is equally critical to digitalization success. Changing the way things are done can be difficult—not just from an operational standpoint, but a psychological one, as well. Employee reluctance, resistance, or pessimism can slow progress and impede implementation. Cultivating a supportive internal culture starts at the top. With the right communication and consistency from management, that positivity will permeate throughout the organization. This unified support helps ensure that everyone involved is pulling in the same direction, greatly increasing your chances of executing an efficient and effective digital transformation.