Data-Driven Manufacturing
by Jason Bullard, on Oct 23, 2023 9:02:06 AM
Solving issues before they have a chance to become costly problems
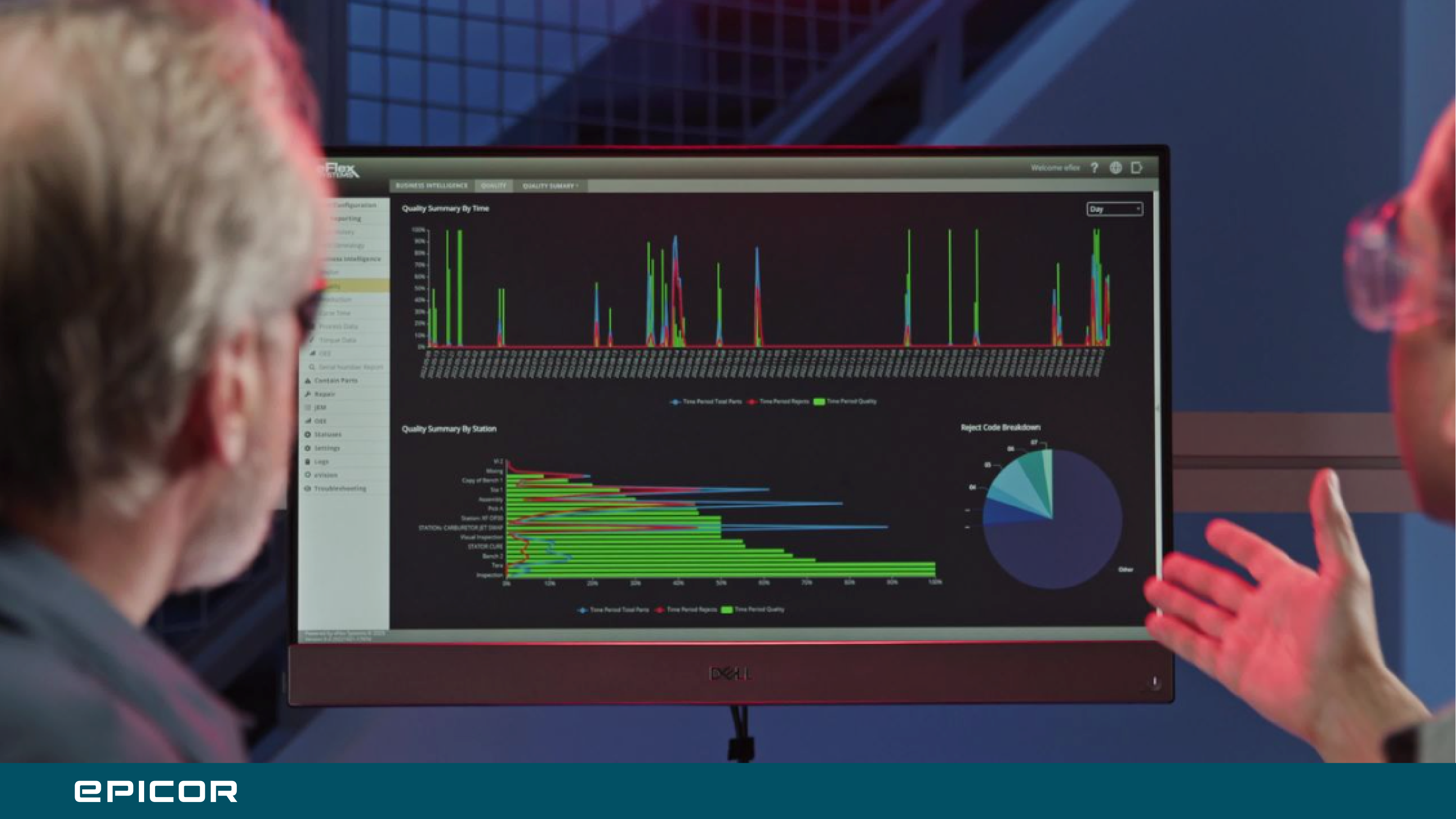
One of the frustrating inefficiencies that has long plagued manufacturers—and one that still presents a problem today for those manufacturers who remain reliant on outdated or legacy controls—is the inability to address quality issues or production problems until after those issues have already incurred a significant cost in wasted time and materials. Correcting problems at the end of a shift (something that some manufacturers still do with a station-to-station collection of written operator summaries or checklists) might allow you to correct the issue before the next shift, but at what cost? If you produced 1200 parts during that production window and a problem began at part number 100, that’s an inexcusably wasteful turn of events.
This kind of antiquated after-action approach to quality control or production efficiency is the result of a lack of visibility into operations and a corresponding inability to put out fires when they occur. This is inconsistent with the principles of kaizen, the Japanese-born philosophy of continuous improvement. One of the core principles of kaizen is to be proactive about solving problems. Clearly, the reactive or even retroactive capabilities of some manufacturers makes this goal impractical or impossible.
With connected process control technologies, however, reactive problem solving becomes, fittingly enough, a thing of the past. The vast volumes of detailed real-time data collected with connected tools and technologies not only yield new insights, but reveal them early enough to facilitate meaningful quality control and error correction almost immediately. The best-connected process control solutions can even anticipate and solve problems before they become problems, with the ability to detect changes in machine or operator performance as well as product quality. By allowing maintenance, replacement, or error correction before small issues become big problems, these systems can save manufacturers an extraordinary amount of time and money.
It’s not only about software, but hardware as well. Manufacturers looking to integrate these game-changing capabilities into their operation should not only embrace new technology solutions, but also the new and updated shop floor equipment that makes such elevated connectivity possible. An older machine press might technically function sufficiently to remain in operation, but it likely lacks the sensors that help ensure that a modern version of the same equipment does not exert the wrong amount of pressure. Upgrading these tools can drastically reduce the time products spend in rework/repair to almost zero.
With standardized process control, creating data insight down to the task level, manufacturers have the visibility they need for improved performance and production of a higher quality product. And because manufacturers can leverage collected information to drive improvements through better training and more efficient processes, they proactively avoid countless errors, both human and otherwise.
How much of a difference can proactive data-driven manufacturing systems make? Simply adding automated pick lights and sensors to parts bins changed a laborious and error-prone hand-selection process that would often take 20-30 minutes to one that operators can now complete in 3-4 minutes, with essentially zero chance of the wrong part being selected. Examples like these show that not only are problems being addressed before they can become real problems, but also illustrate the potentially transformative impact of data-driven manufacturing through connected process control.